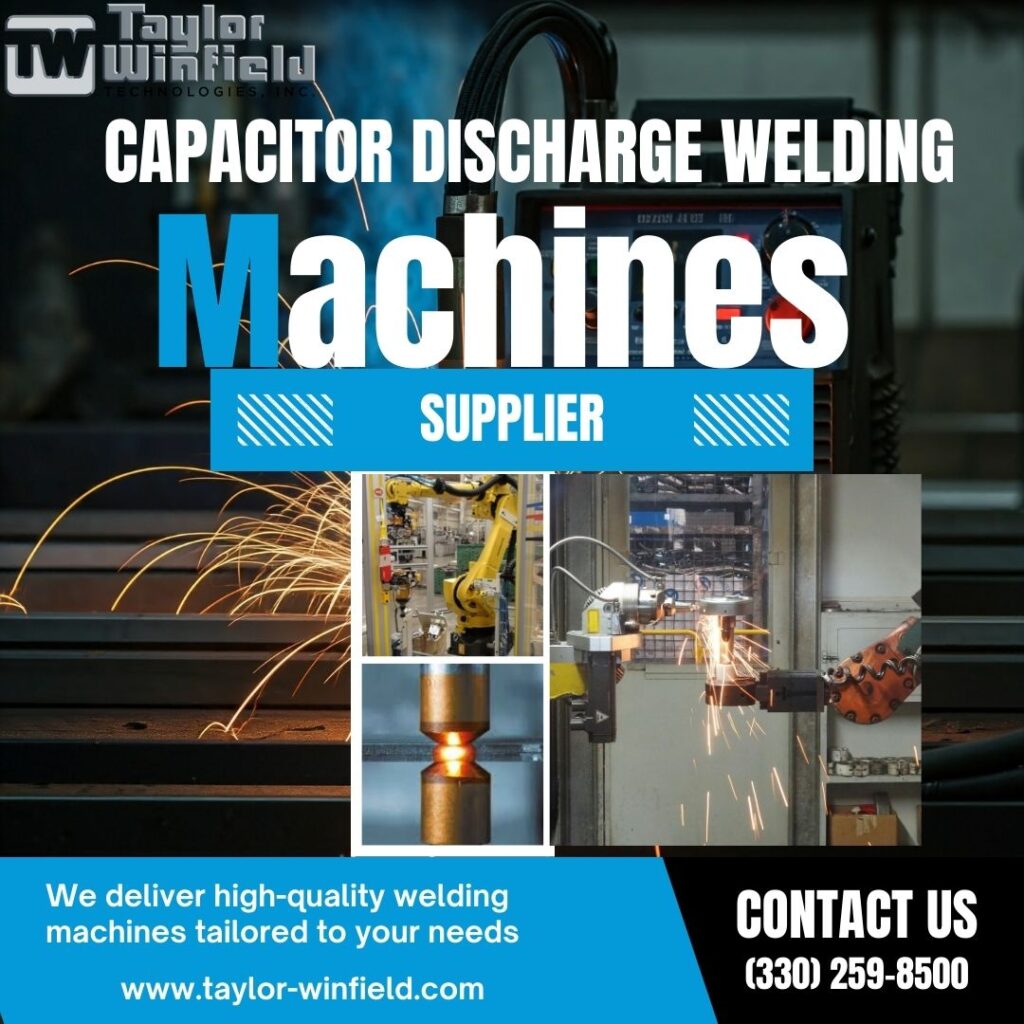
Welding has long been a cornerstone of industrial manufacturing, enabling the construction and production of a vast range of goods, from automobiles to infrastructure. Among the many welding technologies available today, capacitor discharge welding (CDW) stands out for its precision, efficiency, and effectiveness, particularly in applications requiring minimal thermal distortion and high-speed production.
In this article, we explore the significance of capacitor discharge welding machines, their applications, and why choosing the right capacitor discharge welding machine supplier, such as Taylor-Winfield Technologies, can make a substantial difference in the quality and performance of your operations.
What is Capacitor Discharge Welding?
Capacitor discharge welding (CDW) is a process in which stored electrical energy from capacitors is discharged into the workpiece to create a weld. Unlike traditional welding methods that rely on constant heat and pressure over a longer period, CDW utilizes a high-intensity, short-duration discharge to weld metals in milliseconds. This unique welding method results in several key advantages:
-
Precision:
The short welding time significantly reduces the heat-affected zone (HAZ), minimizing distortion and preserving the integrity of the surrounding material.
-
Speed:
CDW is extremely fast, with the welding process occurring almost instantaneously. This makes it ideal for high-volume production lines that require quick welding cycles.
- Minimal Energy Use:
The process is highly energy-efficient because it concentrates the electrical discharge directly into the weld, reducing waste and lowering operational costs.
-
Versatility:
CDW can weld dissimilar metals, making it a flexible solution for industries that use a wide variety of materials.
- Superior Weld Quality:
The controlled nature of the process ensures consistent weld strength and reduces the risk of defects like porosity or cracks.
Given these advantages, CDW is widely used in industries such as aerospace, automotive, electronics, and manufacturing, where precision and speed are critical.
Applications of Capacitor Discharge Welding Machines
Capacitor discharge welding machines are employed across multiple sectors for a variety of applications. Here are some common use cases:
- Automotive Industry: In automotive manufacturing, CDW is used to weld fasteners, studs, and other small components onto larger structures. The speed and precision of the process allow for high-quality welds without damaging sensitive materials, making it ideal for parts like car bodies, exhaust systems, and electronic components.
- Aerospace Industry: In aerospace, weight reduction is critical, and the ability to join lightweight materials such as aluminum and titanium is essential. CDW is perfect for welding these materials, ensuring strong, lightweight joints without adding excessive bulk or weakening the metal.
- Electrical and Electronics Industry: CDW is used to weld electrical contacts, terminals, and other small components where precision and minimal heat impact are vital. The process is ideal for delicate electronic assemblies that could be damaged by traditional welding methods.
- Sheet Metal Fabrication: The ability of CDW machines to weld thin sheet metals without warping or distorting the material makes them invaluable in industries that work with fine materials, such as HVAC or kitchen equipment manufacturing.
- Stud Welding: One of the most popular applications for CDW is stud welding, which is used in industries ranging from construction to electronics. The speed and reliability of the process make it ideal for securing studs, pins, or bolts to a base material without requiring additional fixings.
Why Choosing the Right Capacitor Discharge Welding Machine Supplier Matters
The quality and performance of a capacitor discharge welding machine are crucial to achieving the desired results in any application. Choosing the right supplier can make a significant difference in the efficiency and reliability of your operations. Here are a few reasons why working with a reputable supplier like Taylor-Winfield Technologies is essential:
1. High-Quality Machinery
Suppliers like Taylor-Winfield Technologies offer state-of-the-art capacitor discharge welding machines that are engineered for precision and durability. With decades of experience in developing advanced welding systems, their machines are built to handle demanding industrial environments while maintaining consistent weld quality.
2. Custom Solutions
Not all industries have the same requirements when it comes to welding. A top-tier supplier provides customized solutions tailored to your specific needs, whether it’s for unique materials, specialized parts, or integration into automated systems. Taylor-Winfield Technologies works closely with clients to understand their production challenges and design machines that meet those needs effectively.
3. Expert Technical Support
Even the most advanced machinery needs to be properly supported to perform at its best. Reliable suppliers provide comprehensive technical support and training, ensuring that your team is fully equipped to operate the machines efficiently. In addition, they offer ongoing maintenance services to ensure that your capacitor discharge welding machines continue to run smoothly and with minimal downtime.
4. Innovative Technology
Capacitor discharge welding is a fast-evolving field, and staying ahead of technological advancements is essential. A leading supplier invests in research and development to bring the latest innovations to their products. Taylor-Winfield Technologies, for example, is constantly pushing the boundaries of what capacitor discharge welding machines can achieve, offering cutting-edge features like enhanced precision control, faster cycle times, and more efficient energy use.
5. Compliance with Industry Standards
When choosing a capacitor discharge welding machine supplier, it’s important to ensure that their equipment complies with industry standards and safety regulations. Taylor-Winfield Technologies is known for its strict adherence to quality and safety standards, ensuring that their machines meet all necessary certifications, giving you peace of mind and protecting your investment.
Taylor-Winfield Technologies: Your Trusted Supplier for Capacitor Discharge Welding Machines
This organisation is a leading name in the welding industry, with a strong reputation for delivering high-performance, reliable welding systems. Their capacitor discharge welding machines are designed with precision, efficiency, and ease of use in mind, making them an ideal choice for manufacturers across a wide range of industries. With a focus on innovation and customer satisfaction, Taylor-Winfield is committed to providing clients with the best possible solutions for their welding needs.
Whether you’re in the automotive, aerospace, electronics, or sheet metal industry, Taylor-Winfield Technologies can offer customized capacitor discharge welding machines to suit your specific production requirements. Their machines are built to enhance your manufacturing capabilities, reduce downtime, and improve overall efficiency.
Conclusion
Capacitor discharge welding machines offer a revolutionary approach to joining materials with precision, speed, and efficiency. The right supplier can make all the difference in ensuring that your welding process meets the highest standards of quality and performance. As a trusted supplier, Taylor-Winfield Technologies provides cutting-edge CDW machines that are tailored to the unique needs of your business. By investing in high-quality machinery and expert support, you can enhance your production capabilities and stay competitive in today’s fast-paced industrial landscape.